Builders tackle the complexity of modern factories
When they started work at the Cloverland Farms site in Baltimore City, the Wagman Construction team knew they were digging into a daunting, multi-faceted renovation. Installing next-generation, robotized manufacturing systems in a 1960s dairy plant would involve building a new processing room for equipment that could produce Extended Shelf Life (ESL) products, retrofitting a penthouse, adding three new boilers, fully renovating a laboratory for testing and quality assurance operations, and erecting an exterior steel canopy platform to house a cooling tower, ammonia tower and refrigeration system. And those were just the topline items.

To complicate things further, “there were absolutely no drawings, no as-builts” for the 60-year-old building, said Cory Mummert, Senior Project Manager at Wagman.
Despite the team’s effort to create as-builts, most new phases of the renovation generated surprises. When workers began demolishing the lab, they discovered asbestos fireproofing on the beams, triggering a month-long delay for remediation.
Initial work in the processing room uncovered an unusually thick slab – a six-inch slab above a diamond plate above another eight-inch slab – which added three weeks to the demolition schedule. The room’s ceiling consisted of “hollow-core, precast planks. We had to do a lot of investigative work to establish a safe way to demo these 1,000-pound slabs and get them out of an operating building through eight-foot corridors,” Mummert said.
The team had to coordinate with outside suppliers of specialized equipment, including robotic packaging technologies from Italy, a pneumatic system to deliver milk samples from arriving trucks to the lab, and an infusion skid that connected a steam line and a glycol system to the production area.
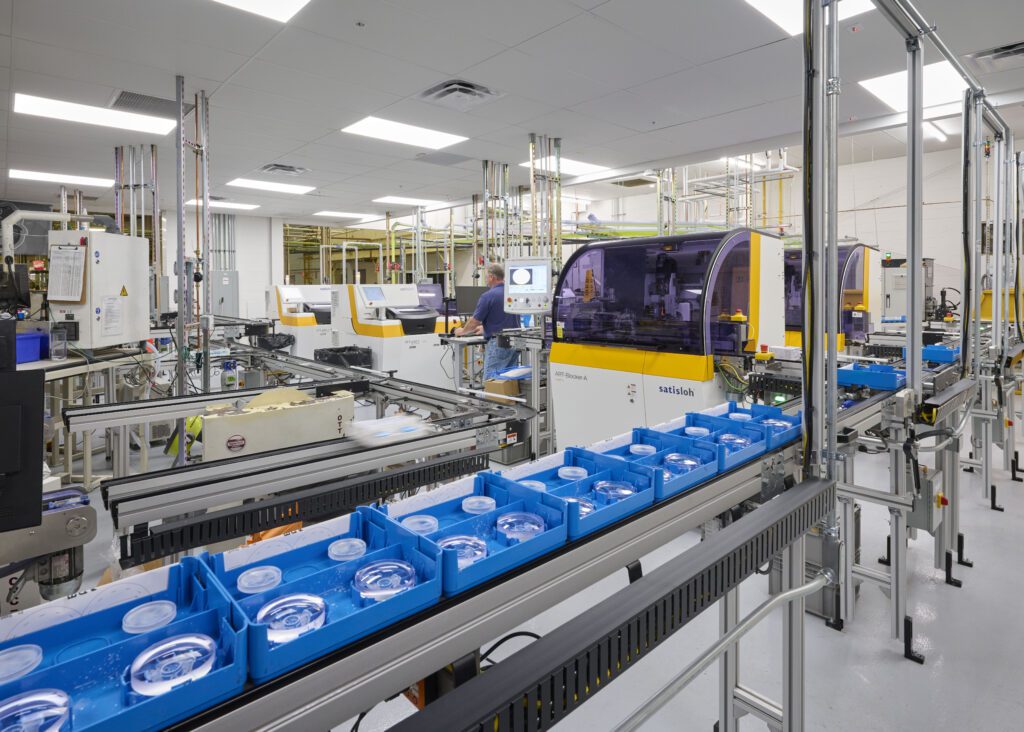
Essilor’s Chesapeake Optical Coating Lab is a 50,000-square-foot, state-of-the-art, prescription glasses’ lens manufacturer and one of very few ISO 9001-certified optical labs in the United States. Photo Wohlsen Construction.
The carefully phased, 13-month renovation also had to support ongoing operations and maintain conditions required by the Food and Drug Administration, “but I loved this project because it kept us on our toes,” Mummert said.
Maryland may not be a hub of massive factories. But the state is home to over 4,000 manufacturers, producing everything from spice mixes, power tools and athletic gear to vaccines, medical devices, military equipment and the batteries used in most satellites.
Heightened interest in reshoring manufacturing and heightened investment through the federal infrastructure package and other funds are prompting many manufacturers to expand and upgrade their operations. For the construction industry, that means more clients are looking to create high-performance, high-tech facilities, often in existing spaces.
From the outside, the Essilor of America plant looks like any other mid-rise, business park building. But inside, Essilor’s Chesapeake Optical Coating Lab is a 50,000-square-foot, state-of-the-art, prescription glasses’ lens manufacturer and one of very few ISO 9001-certified optical labs in the United States.
When Essilor needed to expand its manufacturing capacity, Wohlsen Construction renovated 7,000 square feet of production space and a 1,700-square-foot shed. Working around Essilor’s continuous, three-shift operations, crews demolished existing cafeteria space, built out space to house five new coating machines plus chemical-preparation equipment and installed new process chillers, water and air systems, and rooftop units.
The size of new equipment and the constraints of existing space meant that crews had to conduct inventive demolition and construction, such as temporarily disassembling entire sliding door systems or filling a needed opening in a block wall with an airtight, plexiglass partition, said David Zikorus, Senior Project Manager at Wohlsen.
Crews had to meticulously protect ongoing clean room operations and create additional clean room space with electrostatic flooring, ceiling tiles and other specialty products. They also had to coordinate work with the client’s outside equipment supplier.
“They were bringing in European equipment and we had to connect it to American equipment in the building,” Zikorus said. “The differences between European and American design meant their widgets didn’t always fit into our widgets. Our field guys had to create adapters to make everything work.”
The project team also coordinated closely with factory workers not only to support ongoing operations but to optimize the renovation’s design, he said.
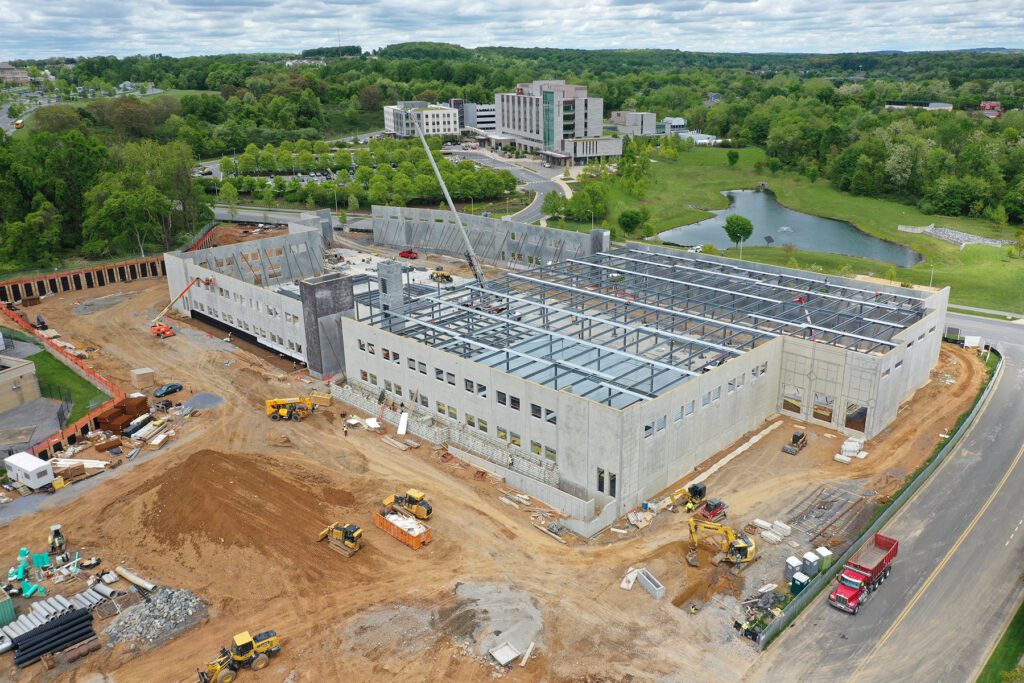
Maryland’s high-tech manufacturers challenge builders to create such facilities as a satellite/communications plant. Photo courtesy of Arium AE.
Many manufacturers who periodically renovate existing space (rather than experiencing a costly disruption by moving to new space), can end up with inefficiencies in their factory design.
The Essilor renovation enabled the company and local staff to improve both the efficiency and comfort of their workspace, Zikorus said.
Despite the preference by many manufacturers to renovate rather than build new space, some Maryland companies are creating manufacturing space from the ground up. In Germantown, The Whiting-Turner Contracting Company is currently building a 140,000-square-foot, tilt-up concrete building for a satellite/communications company.
Most new manufacturing buildings have elevated demands, including heavier, reinforced slabs and expanded power and water supplies. The satellite/communications manufacturer project includes specialized HVAC, temperature controls, humidity controls, power distribution, a clean room environment and access to the roof where the company will install satellite dishes to test their products, said Bill Gnagey, Senior Associate and Director of Business Development at Arium AE, the architecture and engineering firm on the project.
Located on a college campus, the Class A+ manufacturing facility must also serve a second purpose, namely as instructional space and a site for student internships. To ensure the building both serves that purpose and blends into the college campus, “we were given a lot of creative leeway with the design aesthetic,” Gnagey said. “Aesthetically, this building will go above and beyond the look of a normal industrial warehouse.”
Successfully blending manufacturing with an entirely different function inside a single building is a common requirement and challenge within Maryland’s craft beer industry.
Earlier this year, Partner Contracting completed a renovation at Heavy Seas Brewery. As Maryland’s oldest and one of its largest craft breweries, Heavy Seas wanted to alter its Halethorpe building to create a refreshing new space for the public that would “showcase the level and quality of manufacturing that is happening in Maryland,” said David Jaques, President.
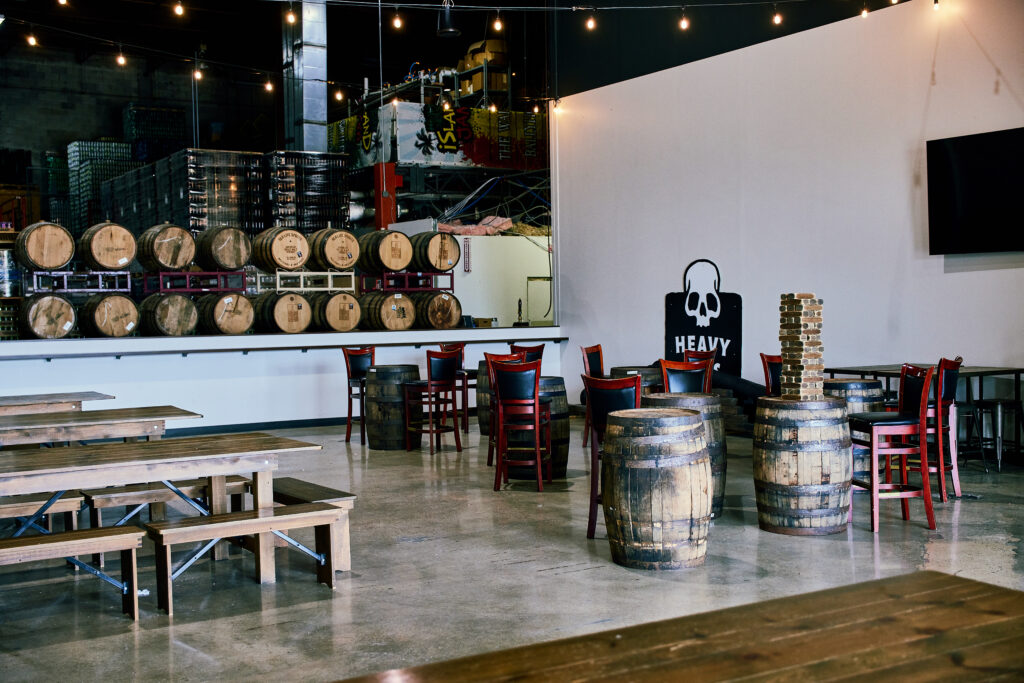
A renovation of Heavy Seas Brewery enabled visitors in the taproom to see some of the manufacturing operations. Photo courtesy of Partner Contracting.
Achieving that goal would require more than new floors, walls, bar, accessories and other finishes in the taproom and games/party rooms. The project which was also designed by Arium AE, would have to make the manufacturing operations more accessible. Crews removed part of the CMU wall dividing the taproom from the brewing area and installed a six-by-six-foot window. They also reconfigured the taproom to open it onto the bottling area, then installed a 4.5-foot-high knee wall to create a drink ledge that would also block access into the bottling area.
“Our main goal was to make sure everyone was kept separate and safe but could see some of the manufacturing operations,” said Tripp Waltemeyer, Project Manager at Partner Contracting. “The knee wall safely opened up a view of the bottling area where there is all that clinking of bottles and cans. You have water dripping down on them and colorful stickers are being applied. It’s exciting to see.”
Meanwhile, the installation of an oversized fan and other ventilation protected visitors from brewery smells.
“We are super proud of the Heavy Seas project,” Jaques said. “It exemplifies the ability of a small business, a small manufacturer in Maryland to thrive and produce great products, and it gives the public an opportunity to see that.”