Mission Driven: Military projects present big challenges, deep rewards
Standing in the basement of Kuhn Hall on Fort George G. Meade, members of a project team lead by The Whiting-Turner Contracting Company searched for a solution to a space challenge.
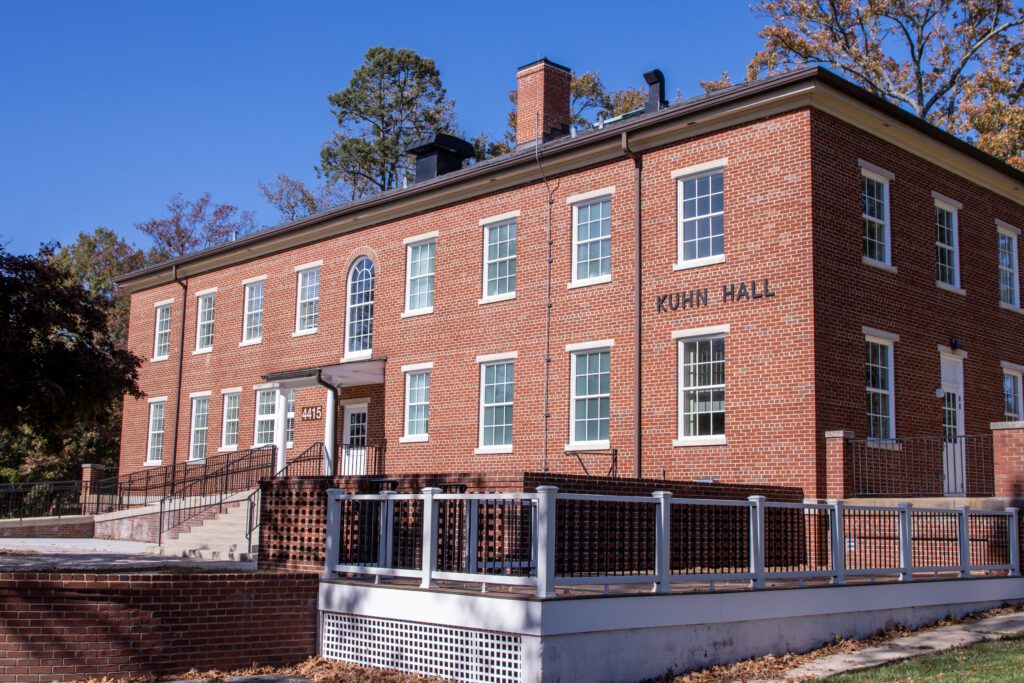
The transformation of the former Distinguished Visitors Quarters by the Fort Meade Alliance and the Fort Meade Alliance Foundation into a modern Education and Resiliency Center for military members, their families and other Fort Meade personnel would require the installation of an elevator. The compact, three-story, 1930s building, however, did not provide the team with sufficient space for an elevator shaft.
Crews would have to dig under the foundation, jack up the building and construct new underpinnings. The operation would have to be completed while other work continued elsewhere in the building. It would also require the project team to find a way to get equipment into and functional within a tight basement space.
Ultimately, workers had to take apart a mini excavator to get it into the building then reassembled it in the basement. Deft operators then managed to dig a six-by-six-foot hole while working inside a 10-by-10-foot room and remove excavation spoils through an elaborate conveyor system.
Construction projects on military installations require rigor, expertise and some high-level problem-solving. Contracts on Department of Defense properties involve meticulous facilities requirements, lengthy contracting processes and challenges with security requirements. Yet contractors say those projects also rank as some of their most fascinating and deeply rewarding work.
Pulling off the interior, gut renovation of Kuhn Hall amounted to “stuffing 20 pounds of potatoes into a five-pound bag,” said Patrick Morgan PE, Electrical Associate at James Posey Associates (JPA).
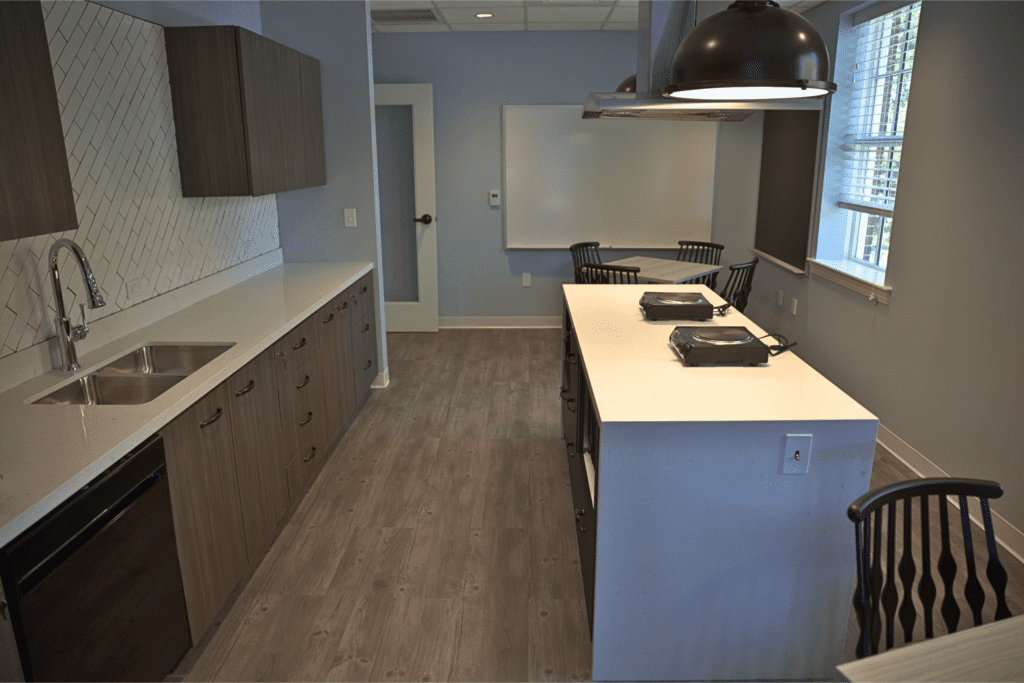
The design for the 9,000-square-foot building called for the creation of multiple offices, classrooms, meeting spaces and a teaching kitchen to support an array of educational and resiliency services, provided by numerous military and community organizations. For JPA, that meant squeezing a lot of modern infrastructure into a tight, historic building.
“Down in the basement, we had a very small room to provide piping and electrical infrastructure so we had to look at compact options and custom equipment in order to reduce the footprint and sneak everything in there,” Morgan said.
The team “made use of odds and ends of space in the building” to accommodate equipment, such as the installation of fire protection infrastructure in a former carport, said Craig Rasmussen PE, Senior Project Manager at JPA.
JPA made extensive use of 3D modeling to design chases, conduct clash detection and keep installations “as flat as possible” in order to optimize ceiling heights, Rasmussen said. “There were constant struggles to get the ductwork, the piping, the structure and the architecture all aligned.”
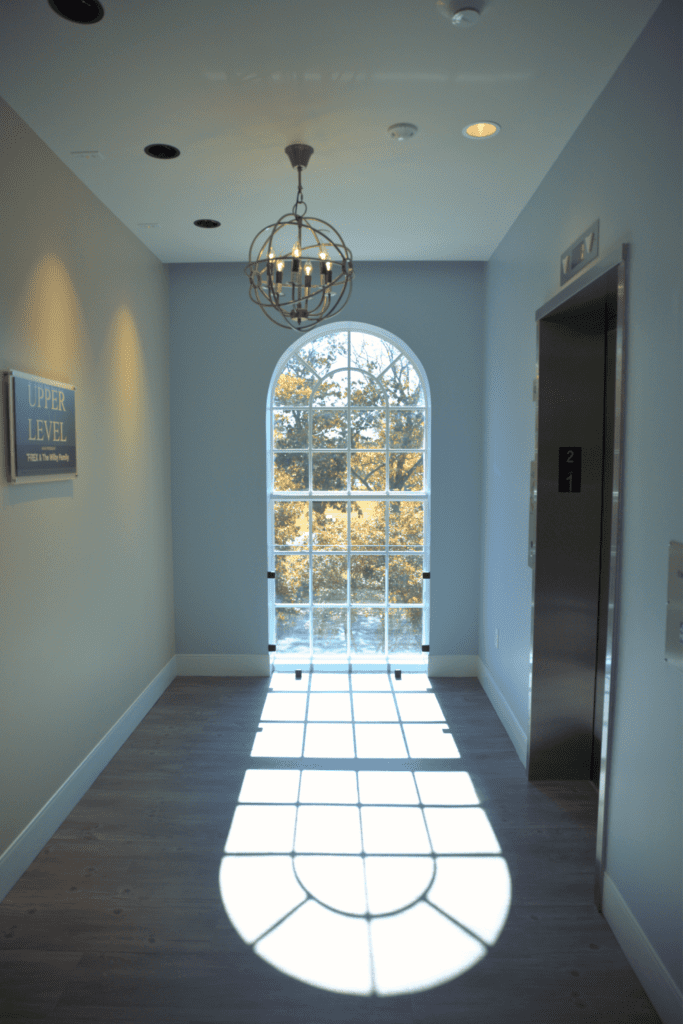
In addition to adding an elevator to the building, the project team also had to construct two new staircases. Available space, however, left barely enough room to fit the structure and achieve the stairway width required by the fire code.
Contractors and designers conducted intensive, old-school coordination to determine exactly where to shave concrete and shift installations in order to build the staircases without impacting sprinkler lines, electrical panels or other infrastructure.
Meanwhile in Annapolis, Whiting-Turner, JPA and other team members were deciphering a different litany of challenges as they constructed the Beach Center, a conference facility at the U.S. Naval Institute.
The plan was to renovate 13,000 square feet of the Naval Institute’s four-story, T-shaped building which opened in 1942 as a hospital and was converted to offices in 1998. The project team would also construct a 5,500-square-foot, curved addition in the area between two arms of the T.
In addition to the inherent challenges of building curved spaces, crews had to contend with a tight site beside a busy road which was the primary emergency services route to the Naval Academy campus. Since closing the road was not an option, the project team devised a plan to place the crane in the middle of what would become the auditorium and build the structure from the inside out. The plan left an opening at the end of the building’s radius that allowed the crew to drive the crane out of the building.
Before construction could even begin, however, the project team had to overcome a major, unexpected hurdle. When actual existing conditions were uncovered at the beginning of construction, the differences from available existing documentation were significant, requiring immediate, creative re-working of sub-slab infrastructure.
“Turns out that [planning based on the documentation] was a big swing and a miss,” said Zachary Haupt PE, Mechanical Associate at JPA.
During three intensive weeks, the project team altered design plans and switched from a partial to a full demolition of the floor slab.
The phased, occupied construction would also require the project team to tie new building systems into existing, legacy systems. Again, the engineers’ work was complicated by “lack of good documentation,” Haupt said. “Some records of existing riser sizes were just plain wrong. Some documents indicated a 1.5-inch pipe when in actuality they were 0.75 or 0.5 inch pipe.”
Those and other errors forced the project team to adjust installation plans, coordinate additional access and outages in occupied space, and complete extensive, custom calculations.
“It is typical for design consultants to have their own spreadsheet calculation tools to figure out sound estimates of what the head loss will be on a piping system,” Haupt said. “We couldn’t do those quick calculations on this project. We had to look at every single linear foot on a branch line to see if it would need to be replaced. These were tough calculations and they had to be completed quickly because this was happening during construction.”
The challenges of construction on military installations, however, drive many companies’ enthusiasm for the work.
Twelve years ago, Matos Builders leveraged its experience constructing laboratories to begin landing DoD contracts. Since then, Matos has worked on numerous medical, semi-conductor and laser labs on installations in Maryland and nearby. It has also completed various other military projects, including physical security installations, office buildouts and replacements of roofs, windows, fuel tanks and other items. In the process of expanding military work to about one-third of its book of business, Matos learned some core lessons about how to approach and excel in DoD projects.
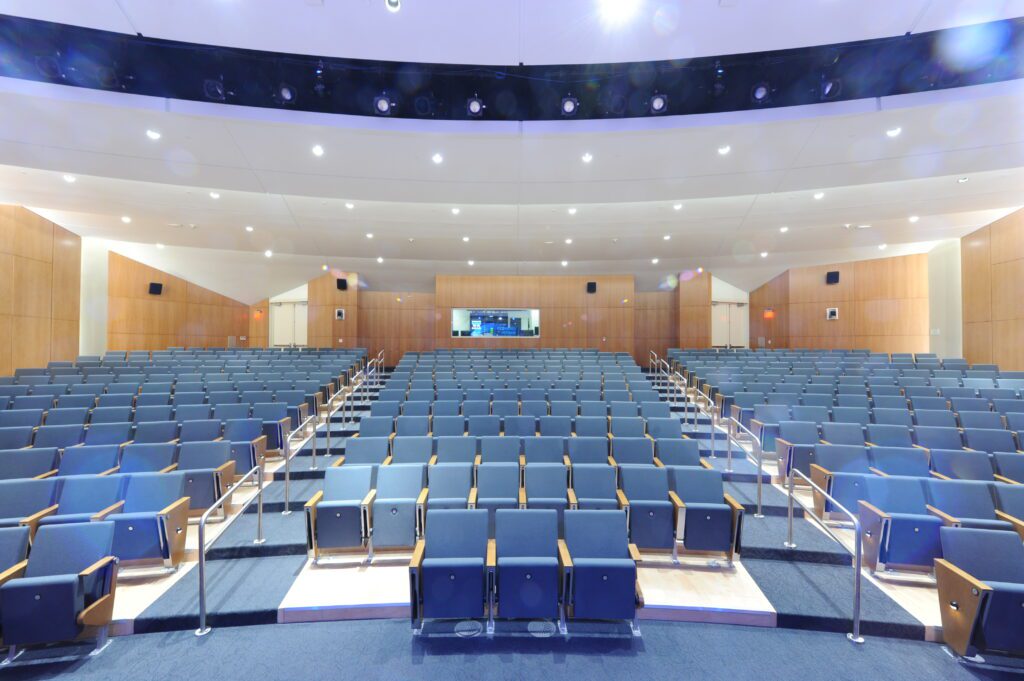
“When we started, we vastly underestimated the security requirements,” said Michael Macsherry, President of Matos Builders. “One of our first projects was renovating the Distinguished Visitors Lounge at Andrews. Every time somebody came through there, we had to stop work and leave the jobsite. We were paying employees to sit offsite in a secure location and do nothing.”
Matos quickly learned to factor security impacts into its budgets and schedules, including the roughly 90-day wait for workers to obtain security badges, the daily delays (often lasting two hours) to get crews and trucks through security and to a jobsite, and the work stoppages triggered by simple things, like restroom breaks. On some sites when an individual needs to go to the restroom, the escort for a construction crew requires everyone to go.
“We figure in an eight-hour day, they are maybe getting five hours of work done,” Macsherry said. “We factor that into our bids and we communicate that to our subcontractors so they don’t get stuck.”
Military contractors have to be prepared for other challenges, said Richard Skayhan, Vice President of Matos. Those include extensive and differing facilities codes and requirements for each branch of service and “the three-letter agencies,” heightened quality control and safety requirements (those prompted Matos to create an in-house QC department and partner with Diversified Safety Services), hazmat and other environmental issues in older buildings, inability to communicate with crews working at secure sites and extraordinary construction requirements in advanced technology facilities.
“But we like the difficult projects because they are exciting,” Skayhan said. “You go to cool places and see cool buildings. Going up to the mezzanine floors where they have their mechanical systems can be mind-blowing.”
Professionals from Whiting-Turner, JPA and Matos all stressed that military projects are deeply satisfying because of the contribution they make to a bigger national mission.
“We are a veteran-owned company and we employ several veterans and military spouses,” Macsherry said. “We take a lot of pride in using our skills as builders to support the mission of the United States military.”